Water Cooled 3D Printed PLA Component [Journal]
- Dat Ha
- Aug 4, 2020
- 3 min read
Updated: Sep 1, 2020
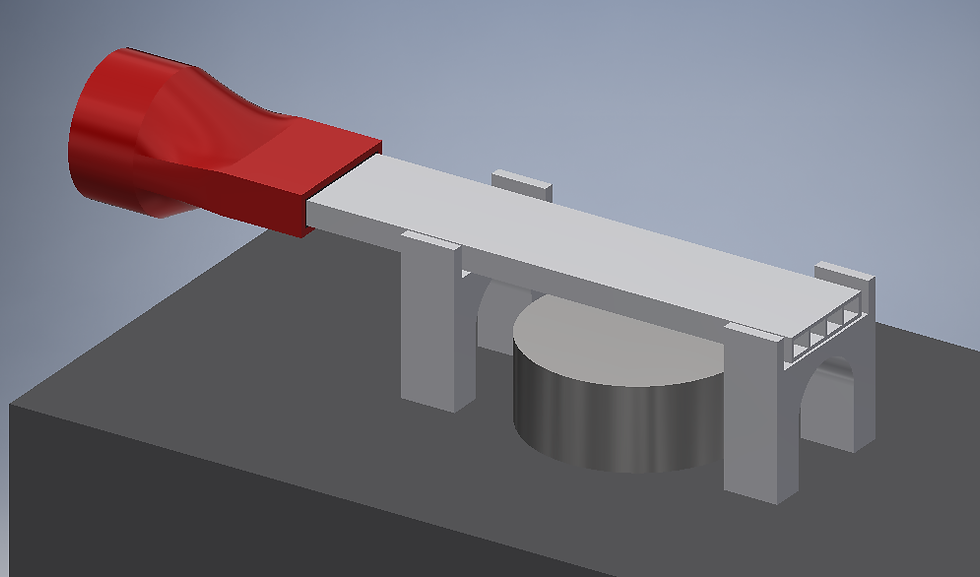
This is a rough journal that I wrote during my experiments of water cooling a PLA 3D print.
This is unformal and it is still considered a draft, but I decided to publish it just to make it public in case anyone was curious.
2020-06-22 (Written on 2020-06-23)
I tried out the first design. As a control, I decided to use some failed prints that are of similar shape and size. The results were partially conclusive. I ran 2 successful tries. In the first one, both remained cooled and therefore my device was not more effective (CHECK VIDEO TO CONFIRM THIS). The second try, the control got warm and soft while the water-cooled device remained cool. This shows that my device was effective.
After the experiments, I redesigned the device so that it was longer and less large. There was no use (I believed at the time) for the device to be that large. Making it longer would make it easier for me to place a brick on it to add a weight. It would also distance the water output from the candle.
2020-06-23
After printing it, I began testing. Note that there were many failures, and so there was only 1 device remaining. That device had a print fault and was not perfect.
Unlike the day before where I used tape to seal the leaks, I did not today which led to the water extinguishing the flame multiple times. I solved the leak between the device and the adapter by placing a little bit of wax there and putting a paper towel to reduce the velocity of any escaping fluid. I also angled the device a towards the adapter (adapter and lower, output and higher) to prevent water passing a piece of plastic that I also used to slow and redirect the fluid. This caused the issue that any slow escaping water from the output would go underneath the device and go down, where it fell into the candle. The mass also played a role in encouraging this effect (CHECK VIDEO NOT SURE).
There was 1 conclusive trial done. The candle was placed under the device for 55 seconds and water passed in it. The water did not run continuously (time between placing candles and pouring water, time for water to go through the tube, I also had to move my phone out of the water that was accumulating below the device. Maybe 1L of water was poured (a lot leaking including when I poured). The device did get a little warm, but it remained rigid. On the other hand, the non-cooled test (same device, but with water drained (might still be a little wet) got warm and started melting. The temperature sensing devices (laser thermometer) did not detect a significant temperature increase, but I could feel that it was significantly. I believe that the thermometer was not properly used by me or it was not designed for such applications and I will believe that my hands were a more accurate sensor in this scenario. This was evident by the melting and of how soft the device got after the flame was removed. This therefore shows, once again that my device worked. A possible error that could have happened is that the device being wet and having a little wax coating, the two substances could have changed the way that it got heated, therefore maybe making my conclusion erroneous for this trial.
2020-06-24
No test done today.
Yesterday, I redesigned the device to include the adapter as part of the piece. Since I was 3D printing the device, doing this was easy. This also should prevent one of the biggest issues I have had with yesterday’s tests: leaks.
Wall thickness increased from 0.7mm to 0.8mm to reduce small printing issues. This was because the shell feature in CAD sets the thickness perpendicularly to a certain point at a wall, but the goal was to have 2 wall layers on the final 3D print. By setting it at 0.8mm, there are at least 2 perimeters everywhere, and some filler at some places. There were many “zits” on the inside of the adapter though.
2020-06-25
Tested the pieces printed yesterday, still small leaks on the body, but less onto the candle. The part where the tube fits in was not the perfect size and had a lot of zits. These factors may or may not have resulted or helped in causing a lot of water to shoot back out of the female input of the device. The tube was not straight also which could have caused issues.
One of the 2 prints broke due to it being very fragile.
During testing, the water cooled performed as expecting, getting a little warmer than the water, nothing significant. When no water was passing through, the parts melted. Those parts had some water residue in there. I could hear the water boiling.
Comments